An intensive professional development training course on
DMAIC Essentials
Building a Data-Driven Problem-Solving Framework
Why Choose DMAIC Essentials Training Course?
This DMAIC Essentials: Building a Data-Driven Problem-Solving Framework online training course is designed to provide participants with a comprehensive understanding of the DMAIC (Define, Measure, Analyze, Improve, Control) framework, which is the core methodology used in Lean Six Sigma. Participants will learn how to apply a structured, data-driven approach to problem-solving, enabling them to identify root causes of process inefficiencies, develop solutions, and ensure sustainable improvements. The course focuses on practical tools and techniques to build a robust framework for continuous improvement.
What are the Goals?
By the end of this AZTech online training course, participants will be able to:
- Understand the fundamentals of Lean Six Sigma and the DMAIC methodology
- Learn how to define problems clearly and set measurable goals
- Develop skills to measure and analyze process performance using data
- Identify and implement effective improvement strategies
- Ensure long-term sustainability of process improvements through control mechanisms
- Gain hands-on experience with essential DMAIC tools and techniques
Who is this Training Course for?
This online training course is suitable to a wide range professionals but will greatly benefit:
- Professionals involved in process improvement, quality management, or operational excellence
- Individuals looking to enhance their problem-solving skills using data-driven methods
- Team leaders and managers responsible for driving continuous improvement initiatives
- Employees from any industry interested in building a strong foundation in Lean Six Sigma
How will this Training Course be Presented?
This AZTech online training course will utilise a variety of proven highly interactive adult learning techniques to ensure maximum understanding, comprehension and retention of the information presented. This includes facilitated group and individual exercises, case studies, role-play, and videos.
The Course Content
- Overview of Lean Six Sigma: History, Principles, and Benefits
- Introduction to the DMAIC Framework and Its Application in Various Industries
- Defining the Problem: Understanding the "Define" Phase
- Identifying Critical-to-Quality (CTQ) Metrics and Setting Project Goals
- Tools for the Define Phase: SIPOC Diagrams, Project Charters, and Stakeholder Analysis
- Case Study: Defining a Sample Project and Setting Objectives
- Introduction to the Measure Phase: Collecting and Understanding Data
- Identifying Key Performance Indicators (KPIs) and Process Metrics
- Tools for Data Collection: Process Mapping, Flowcharts, and Value Stream Maps
- Measurement System Analysis: Ensuring Accuracy and Reliability of Data
- Basic Statistical Tools for Measuring Process Performance: Mean, Standard Deviation, Control Limits
- Practical Exercise: Collecting and Analyzing Data for a Sample Process
- Introduction to the Analyze Phase: Using Data to Diagnose Problems
- Root Cause Analysis Techniques: Cause and Effect Diagrams, 5 Whys
- Data Analysis Tools: Pareto Charts, Scatter Diagrams, and Correlation Analysis
- Hypothesis Testing: Identifying Relationships Between Variables
- Process Capability Analysis: Understanding Cp and Cpk
- Practical Exercise: Conducting Root Cause Analysis and Hypothesis Testing on Sample Data
- Introduction to the Improve Phase: Designing and Testing Solutions
- Creative Problem-Solving Techniques: Brainstorming, Benchmarking, and TRIZ
- Lean Tools for Process Improvement: Kaizen, 5S, and Poka-Yoke
- Implementing Process Changes: Planning, Testing, and Piloting Solutions
- Cost-Benefit Analysis: Evaluating the Impact of Proposed Improvements
- Practical Exercise: Developing and Testing Solutions for a Process Improvement Case
- Introduction to the Control Phase: Ensuring Long-Term Process Stability
- Tools for Process Control: Control Charts, Monitoring Systems, and Audits
- Standardizing Improvements: Documentation and Training
- Creating a Control Plan: Setting Up Process Monitoring and Response Mechanisms
- Leadership in Continuous Improvement: Driving a Culture of Accountability
- Practical Exercise: Creating a Control Plan for Sustained Improvements
- Final Review and Certification Preparation
Certificate and Accreditation
- AZTech e-Certificate of Completion for delegates who attend and complete the online training course
In Partnership With
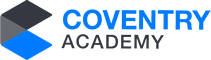
Do you want to learn more about this course?
© 2024. Material published by AZTech shown here is copyrighted. All rights reserved. Any unauthorized copying, distribution, use, dissemination, downloading, storing (in any medium), transmission, reproduction or reliance in whole or any part of this course outline is prohibited and will constitute an infringement of copyright.
Frequently Asked Questions
Yes, we offer tailored corporate training solutions to meet your organization’s specific needs. Please contact us at info@aztechtraining.com or call +971 4 427 5400 for more information.
Our training programs are hosted at luxurious five-star hotels in prestigious destinations across the globe. Some of our popular locations include Dubai, London, Kuala Lumpur, Amsterdam, New York, Paris, Vienna, and many other iconic cities.
The training fees include full access to the training venue, along with comprehensive training materials to enhance your learning experience. Additionally, participants will be provided with writing supplies and stationery. To ensure comfort and convenience, the fee also covers lunch and refreshing coffee breaks throughout the duration of the course.
Once your registration is successfully completed, you will receive a confirmation email within 24 hours. This email will contain your registration details, invoice, and the necessary joining instructions for the course.
There are several convenient ways to register for our training programs:
- Online: Explore our training calendar, choose the course that suits your needs, and click the “Register Now” button on the course details page.
- Email: Share your details, including your name, organization, email address, and selected course, by sending an email to info@aztechtraining.com
- Phone: Reach out to us directly at +971 4 427 5400 or +971 4 427 5407, and our team will guide you through the registration process.